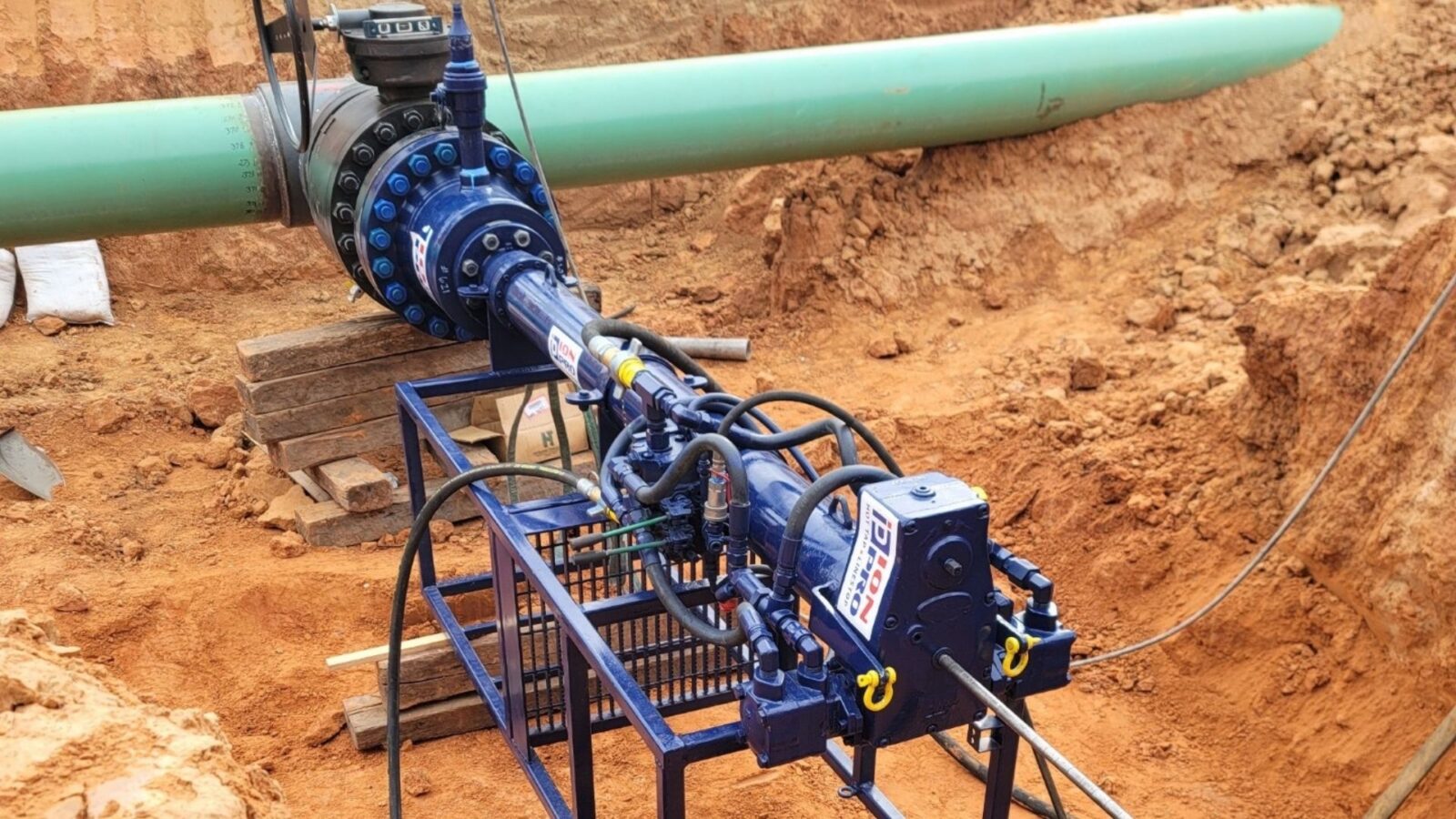
Requirements in Executing a Hot Tap
1. Introduction
This article details the technical and safety requirements for executing a hot tap on hydrocarbon pipelines, piping or tanks.
Hot tapping is a method of making a new connection to an existing pressured pipeline or vessel without interrupting or emptying that section of pipe or vessel. This means that a pipeline can continue to be in operation while maintenance or modifications are being executed.
Another definition According to API RP 2201: Hot Tapping is a technique of attaching a mechanical or welded branch fitting to piping or equipment in service and creating an opening in that piping or equipment by drilling or cutting a portion of the piping or equipment within the attached fitting.
Hot tapping has found wide application in the oil and gas sector. It is often difficult to shut down pipelines due to disruptions it causes in product supply to customers and other facilities. Hot tapping can be used to tie in new connections to an existing pipeline in operation without disruption to flow. And in combination with line plugging can be used to divert flow around a pipeline or piping section that is under repair or maintenance.
2. Critical Analysis Justifying Hot Tapping
As a prerequisite to any hot tap operation, a detailed job analysis encompassing both safety and technical considerations is performed.
A hot tapping operation is a highly safety-sensitive activity and should not be taken as a routine operation. It should only be performed if a facility shutdown is not feasible – an assessment that takes in various considerations, such as:
- Safety: Hot tapping involves hot work, i.e. welding on pipelines, piping or tanks in operation. And so, a proper hot work risk assessment must be done. Safety is the most critical element in every hot tapping operation. If the safety of the personnel and the environment is not guaranteed, hot tapping shall not be performed. Safety mentioned here also include threats that may arise from pollution or release of toxic product in case of hot tap failure.
- Condition of the piping, pipeline or tank to be tapped: The condition of the equipment or piping must be critically analysed to determine if it is safe to perform the hot tap. Equipment or pipelines that are subject to deterioration beyond a set limit shall not be tapped.
- System Configuration: The configuration of the system must be such that hot tapping can be performed without any hindrance. This is usually a more critical criteria for piping configurations and tanks than for pipelines. Where access to the line is restricted, hot tapping should not be performed. This includes the surrounding environmental conditions such as soil conditions, water tables, vegetation overgrowth, etc.
- Operating conditions of a pipeline, piping or tank. As will be discussed later, there are various operational limitations to hot tapping such as fluid temperature, pressure, the velocity of flow, etc. The operating data of the system must be critically analysed to ensure that hot tapping can be successfully executed within these parameters.
- Availability of a suitable hot tapping machine: The available machine to perform the hot tap must be able to execute the task successfully. Machine selection is crucial because the selection of the wrong machine could result in a failed hot tapping operation. The machine must be able to work under the operating conditions such as temperature, pressure, flow rate etc. If a machine that can effectively operate under all identified conditions is not available, hot tapping shall not be performed.
- The economic aspect of the hot tap operation must be thoroughly evaluated. A situation whereby the cost of hot tapping is significantly higher than the cost of the shutdown and routine maintenance should be avoided. See our article on this site that expands on this economic evaluation of a shutdown vs hot tapping.
- Welding Suitability. Can safe welding of the hot tap fitting be performed on the pipeline? Can welding be performed on the pipeline at the operating conditions and material of the tank or pipeline/piping? This must be justified before performing a hot tap.
- Regulatory requirements. All regulations (be that industry codes, local bylaws, etc.) must be carefully evaluated before performing any hot tapping operation and must not proceed if the regulations are not met.
3. General Safety Restrictions
Although over time, there have been significant improvements in hot tapping technology, there are still several restrictions which aim at increasing the safety of the process.
It must be noted that these restrictions vary among companies and are also dependent on the capability of hot tap machines and personnel.
Typically, hot tapping should not be performed on:
- Pipelines, piping or storage tanks that contain a mixture of flammable gas and air
- Heat exchangers or pressure vessel
- Jacketed storage tanks or piping
- Storage tanks or piping that requires Post Weld Heat Treatment. If Post Weld Heat Treating is required, further analysis and consultation with professionals shall be performed
- Storage tanks and piping containing unsaturated hydrocarbon that undergo exothermic decomposition due to high temperature that will result from welding activities. These hydrocarbons include ethylene, propylene, etc.
- The decks, roofs, floating roofs or pontoons of storage tanks
- Cladded pipes or tanks, unless approved after critical examination by qualified personnel. However, hot tapping may be performed on internally flow coated pipes or equipment
- Pipelines or tanks when the fluid content is below 0 Celsius (32 Fahrenheit) or above 200 Celsius (392 Fahrenheit) unless permitted by the client after critical evaluation of the tapping operation
- Equipment under vacuum, i.e. pressure less than atmospheric pressure unless a thorough evaluation by engineering
- Equipment and piping containing hazardous materials. As defined in SHELL DEP 31.38.60.10-Gen, Section 3.2, Table 1, hazardous materials include Acetylene, Acetonitrile, Butadiene, Caustic soda / Sodium Hydroxide, Chlorine, Hydrogen sulphide, Hydrofluoric acid, Oxygen, Propene (Propylene), Propene oxide, Sulphuric acid.
4. Documentation Required in Executing Hot Tapping
Before executing a hot tap, detailed planning and design shall be performed. This shall entail preparing different documents which are reviewed and approved by the client and other stakeholders. Some of the documentation to prepare include:
- Design documentation. Material selection reports, wall thickness calculations, etc. The material selection report shall show the reasons for selecting the materials, the compatibility of the material to the pipe, resistance to corrosion, etc.
- Drawings. The drawings to be prepared shall include general arrangement drawings of the piping network, sections and details, etc.
- Material Take-off. This is a document that will aid the procurement of all materials required to execute the hot tap successfully. It will show the required quantities of valves, bolts and nuts, flanges, pipes for branch connection, etc.
- Safety plan and documentation which shall include a detailed Job Hazard Analysis. The safety plan should, at minimum, cover escape routes, firefighting, safety equipment, gas detectors and first aid facilities.
- Transportation procedures. Shall cover how the hot tap machines, components and personnel will be transported to and from the site. This can become crucial if the hot tap location is remote or hard to reach.
- Site preparation procedures. For hot tap locations in congested areas, the site shall be cleared. In the absence of an access road to the hot tap location, temporary roads shall be created (if feasible). For buried pipelines excavation shall be carried out around the pipeline.
- Hot tapping procedures. The procedure shall indicate the general information about the activities, including the angle of tap, machine operation procedure, etc.
- Welding procedures. The welding procedure is a critical document showing the type of welding, type of electrodes to use for welding, welding current, requirements for preheating, welding temperature, welding machines, etc.
- Non-Destructive Testing (NDT) procedures. This document usually will highlight how the welded joints integrity shall be validated. It may cover activities including hydrotest, UT, MPI, etc.
- Hydrotest procedures. This may be part of the NDT Procedure or a stand-alone document. This will show the test pressure, medium to use for the test, duration of the test, etc.
- Hot tap checklist. A summary of all the activities that have to be completed before the commencement of hot tapping. It is usually in a tabular form with activities completed checked and the personnel responsible indicated.
- Hot tapping close-out report. After successful completion of a hot tap the close-out report is a summary of all activities that where performed, a summary of lessons learned etc.
5. Hot Tapping Requirements
This section highlights some of the essential requirements before performing hot tapping operation. Although each hot tap is unique and should be evaluated on merit, these points do give a general overview.
5.1 Hot Tapping on Pipelines or Piping
Tapping into pipelines and piping is the most common type of hot tapping operation. Some requirements are:
- The pipe material and the fittings used for the hot tapping operation shall be compatible with the material of the run pipe.
- The pipes and fittings shall have a rating equal or higher than that of the existing run pipe.
- Welding procedures shall be prepared and reviewed by an experienced engineer to confirm that the welding can be successfully performed on the pipeline or piping.
- Hot tapping shall be performed preferably in position vertically downward on horizontal pipelines. Before an angled hot tap is performed a detailed job hazard analysis and technical analysis shall be performed.
- Hot tapping and welding should not be performed on flare/vent lines because there is the possibility of oxygen ingress, thereby leading to the formation of flammable mixture. If tapping must be performed on flare lines, it must be confirmed that the line is free of oxygen ingress – if this cannot be confirmed the line must be continuously purged with inert gas or steam during a welding operation. Gas detectors shall be used to check continuously for oxygen and other hazardous gas ingresses.
5.2 Requirements for Tapping into Tanks or Vessels
The main danger in welding on the exterior of a tank or vessel is the ignition of a flammable atmosphere in the vapor space above the liquid level.
There are additional requirements that must be fulfilled to perform hot tapping into a tank or vessel successfully. Some of these requirements are clearly stated in section 9.1 of API RP 2201 -below is a summary of these requirements:
- Welding on the exterior of the tanks shall not be performed unless there is a procedure on the ground to prevent flammable gas/vapor from reaching the vicinity of the welding location. Reliable gas detecting devices must be located at a strategic location. Work shall be stopped immediately when gas/vapor is detected.
- There must be mitigation for every identified possible hazard. Hazards may result from
- Tank venting which may circulate vapor around the location where welding is performed. These vapor results in the formation of a flammable atmosphere around the welding location.
- Overflowing of products within the tank which may result in spillage of products into the welding area.
- Inadvertently allowing the level of liquid in the tank to fall below the welding point. The welding point is not the direct point of welding alone but a defined region around the weld point. When the liquid in the tank falls below the welding point, the heat sink provided by the liquid is lost thereby exposing the vapor space in the tank to the welding point, which is a possible source of ignition.
- Welding shall not be performed above the liquid level on a cladded tank or double-walled tank unless approved by qualified personnel.
- The minimum liquid level above the point of welding shall be 3ft as recommended by API RP 2201 and ExxonMobil GP 03-01-04. SHELL DEP 31.38.60.10-Gen also recommends 39 inches.
- As much as possible, there should be no flow into or out of the tank.
- Welding shall be performed by qualified personnel, preferably with previous experience in welding on live pipelines.
- During welding, burn-through the tank or vessel wall must be prevented. Adequate precautions, including heat/temperature control, must be put in place.
- Hot tapping or welding activities on floating roofs, pontoons, or decks are prohibited. These areas of a tank are subjected to flammability hazards.
5.3 Other Requirements for Considerations
5.3.1 Welding Requirements
A welding procedure shall be developed for the hot tap welding job. All welders shall be qualified per applicable codes and specifications. Consideration may be given to welders with previous experience. As stated in API RP 2201 section 6.8, welding shall not be permitted closer than 18inches to a flange or threaded connection or approximately 3inches to a welded seam (including a longitudinal seam of welded piping) unless determined by an engineering review to be acceptable. All welds shall be visually inspected and tested before connection of the hot tap machine. Dye Penetrant Testing, Ultrasonic or Magnetic Particle Inspection (MPI) may also be utilized; however, pressure tests may be used to validate weld integrity.
5.3.2 Weld Testing
Welded joints must be tested to validate their integrity. If the temperature of the piping, pipeline or tank permits it, a hydrotest should be used to test welded joints per applicable codes. The test pressure should be a minimum of 10% more than the operating pressure; however, if an internal collapse is envisaged, the test should not exceed 10% of the operating pressure. The test pressure may be reduced as per applicable codes. If the temperature does not permit a hydrotest, air or nitrogen with soap solution may be used on the weld.
5.3.3 Process Fluid Velocity Requirements
Hot tapping or welding shall not be performed on piping or pipelines under no-flow condition. When there is no flow, there is a possibility of hazardous gas accumulation. However, when there is flow the heat is carried from the welding location, reducing the possibility of an explosion. Unless determined otherwise by qualified personnel, the flow velocities below are recommended for pipelines or piping.
The minimum recommended flow velocity for gas pipelines or piping as per SHELL DEP 31.38.60.10-Gen is 1.3 ft./s, which is also the recommended flow velocity as per ExxonMobil GP 03-01-04.
For Liquid Lines, the minimum recommended flow velocity as per SHELL DEP 31.38.60.10-Gen is 1.41ft/s.
Note, when the flow rate is too high, there is a tendency of rapid cooling of the welding area, which will affect the welding process and weld quality.
The maximum recommended flow velocity for gas piping or pipelines as per SHELL DEP 31.38.60.10-Gen is 30ft/s while 32.8ft/s is recommended flow as per ExxonMobil GP 03-01-04.
For Liquid Lines, the maximum recommended flow velocity as per SHELL DEP 31.38.60.10-Gen is 5.75ft/s while 16.4ft/s is the recommended flow velocity as per ExxonMobil GP 03-01-04.
5.3.4 Pressure Requirements
All hot tapping machines have pressure ratings at which they can operate effectively. The pressure rating of the machine must be confirmed before the start of hot tapping. The operating pressure of the pipeline must be below the maximum pressure rating of the hot tap machine.
Also, the maximum pressure resulting in the pipeline during the operation should not be higher than the maximum allowable pressure. The maximum allowable pressure can be calculated from ASME B31.4 for liquid pipelines, ASME B31.8 for gas pipelines and ASME B31.3 for process piping. Consideration shall be given to increase in temperature resulting from welding activities in calculating the maximum allowable pressure.
For safety reason, as recommended in SHELL DEP 31.38.60.10-Gen hot tapping shall not be performed on the pipeline when the fluid pressure exceeds 1015 psi. However, there are hot tapping machines rated for ~1450 psi.
5.3.5 Hot Tapping Loads
External loads are a significant concern when performing hot tapping. All external load effects on the pipeline must be carefully analysed and mitigated. When performing hot tapping the weight of the machine and personnel performing activities may be evenly or unevenly distributed on the pipeline, which can cause pipeline failure. All lines to be hot tapped must be properly supported to counter the effect of external loads. Also, when performing this analysis, the corroded or as-is state of the pipeline should be used to perform the analysis.
5.3.6 Minimum Wall Thickness of Pipeline (Run Pipe)
Before performing a hot tap on a pipeline, piping or tank, the wall thickness shall be confirmed. This may be confirmed utilizing Ultrasonic Thickness measurement.
The measured wall thickness shall be used to run an analysis to confirm that the pipe can withstand all loads resulting from operating conditions and external loading resulting from hot tapping.
Also, the thickness of the pipeline goes a long way in influencing the success of the hot taping operation. For pipelines with thickness less than ¼ in the probability of burn-through occurring is very high. However, this may be mitigated to an extent by maintaining an appropriate fluid flow rate, using electrodes with a diameter of 3/32 in or smaller for the first weld pass to limit heat input, etc.
Hot tapping should only start after wall thickness verification has been performed.
5.3.7 Minimum Thickness of Branch Connection
The new pipeline to be connected using hot tapping shall be analysed for all loads after its wall thickness has been calculated. Generally, the wall thickness may be calculated as per ASME B31.4 for liquid pipelines, ASME B31.8 for gas pipelines or ASME B31.3 for process piping.
5.3.8 Temperature Considerations
Allowable temperature shall be considered for both hot tapping machine, fittings and pipeline.
There are hot tapping machines with the capacity to handle temperature up to 300oC.
The maximum metal temperature resulting from hot tapping operation shall be critically examined by qualified personnel. Also the minimum surrounding temperature should be evaluated prior to commencement of welding activities. As recommended by API RP 2201 Section 6.7, welding should not be performed when atmospheric temperature is colder than -50oF (-45oC) unless special precautions are taken. These precautions include providing temporary shelter for welding, providing space heaters.
Welding procedure shall be developed indicating if preheating is required, the electrodes to be used for welding, etc.
The maximum temperature resulting from welding shall be estimated. This shall be estimated using the actual wall thickness of the pipe. The maximum temperature shall take into account the reaction of the fluid transported.
5.3.9 Hot Tap Location
Selecting the location of the hot tap is crucial. Hot tap locations shall be readily accessible and free of obstructions.
Hot tapping shall only be performed upstream of rotating equipment (pumps, compressors, etc.), control valves if there are filters, strainers or traps installed downstream of the hot tap location before the equipment.
5.3.10 Hot Tap Valve or Block Valve
Hot Tap valve shall be appropriately sized to suit the branch connection required. Valves used shall have a rating equal or higher than the existing piping or pipeline rating and shall be full port. Consideration shall be given to sandwich valves; however, gate valves and ball valves can be used. All valves, bolts, nuts and gasket shall be new because they may form part of the system. All valves shall be tested as per applicable codes and standards, including a test for seat leakage.
5.3.11 Hot Tapping Machine
Hot tapping machines will be of appropriate rating in terms of temperature and pressure. It is required that the hot tapping machine must be centred on the valve and aligned with the fitting to ensure uninterrupted cutting of the coupon.
One key factor that must be considered when selecting a machine is the Total Travel Distance of the machine. This is specific to each machine.
Before the start of hot tapping, it shall be confirmed that the selected machine can travel the required distance from the hot tap valve until the entire coupon is cut.
Total Travel Distance may be estimated using the below formula. This formula should be modified to suit each application. For illustration purposes assume the Position of the Cutter just after Cutting the entire coupon and a minor travel distance to ascertain that coupon has been cut.
TTD = VL + FL + CL + PBL
TTD = Total Travel Distance
Where VL = Length of Hot Tap Valve
FL = Nozzle Length (Height of the Flange Above the Fitting Header)
CL = Cutter Length
PBL = Length of Pilot Drill Bit Ahead Cutter
6. Typical Hot Tapping Checklist
As stated in previous sections, hot tapping is a high safety-sensitive operation requiring multi-disciplinary activities. Before commencing the operation, some considerations shall be fulfilled. These considerations are clearly stated in API RP 2201 and other companies’ specific regulations.
The Checklist below is an extract from API RP 2201; therefore, all referenced sections in the Checklist are to API RP 2201. The attached Checklist should be modified to suit each hot tap job to be performed.
EACH OF THE FOLLOWING CONSIDERATIONS SHOULD BE SATISFIED BEFORE STARTING THE HOT TAP | Date | Time | InitialsChecked by | |
1 | Review/follow the hot tap machine manufacturer\’s operating instructions. | |||
2 | Have the contents of the line or vessel to be hot tapped or welded been assessed, and MSDSs reviewed for health hazards, to assure procedure is appropriate? | |||
3 | Is the material in the line or vessel stable under heated conditions? | |||
4 | Has the connection been designed per Section 6 requirements? | |||
5 | Do the flanges, bolts, gaskets, pipe, and valve to be installed meet the code for the line or vessel to be hot tapped? | |||
6 | Has the welding procedure specification been developed as covered in this standard? | |||
7 | Have approved work permits (e.g., Hot Work, Hot Tap, Entry) been obtained? | |||
8 | Review manufacturer\’s instructions to ensure that the hot tapping machine has suitable pressure, temperature ratings, and adequate cutter travel for this job. | |||
9 | Has the valve been pressure tested and the cover fitted to assure that it will work and fit correctly? | |||
10 | Has the exact location of the hot tap been identified and marked on the line or equipment? | |||
11 | Is the area to be hot tapped located on a line in which flow has been established or below the liquid level of the tank or vessel? | |||
12 | Has the area to be welded been inspected for thickness and freedom from existing welds, laminations, hydrogen attack, or other metallurgical imperfections? | |||
13 | Are tests and inspections current? | |||
14 | If laminations or defects have been found, has a thorough engineering evaluation been made by a qualified person to determine if and how to proceed with the work? | |||
15 | Has the metallurgy of the line or vessel been established, and is it compatible with the connecting fitting? | |||
16 | Can the welding and tapping area support the weight of the hot tapping machine, and is there adequate hoisting and support for the hot tapping machine and subsequent piping? | |||
17 | If PWHT of the welded area is required, was an appropriate review conducted per 6.6. | |||
18 | Is there sufficient external clearance to install the hot tapping machine and extract the cutter through the valve? | |||
18 | Is there sufficient internal clearance to retract the cutter and coupon through the valve? | |||
19 | Is the hot tap fitting of the proper length to accommodate the operation of the hot tapping machine? | |||
20 | Have oxygen, combustible gas, and atmosphere contamination tests been conducted in the hot tap area? | |||
21 | Has a dedicated fire watch person been assigned and appropriate training and firefighting equipment provided? | |||
22 | Has the Fire Watch person been provided with a list of duties as outlined in Table 2? | |||
23 | Are all personnel in the area equipped with appropriate personal protective equipment? | |||
24 | Is there adequate storage area and room for operational needs and emergency access or egress? | |||
25 | Has a procedure been prepared and in place to isolate the work area in the event of a failure and material release? | |||
26 | Are personnel trained to implement the contingency procedure? | |||
27 | Have the requirements been defined for weld inspection and pressure testing, and is all of the testing equipment on hand and in good working condition? | |||
FIRE WATCH DUTIES INCLUDE: | ||||
1 | Being able to communicate effectively with personnel in the area | Date | Time | InitialsChecked by |
2 | Watching for fires in all exposed areas | |||
3 | Knowing how to use the assigned fire suppression equipment | |||
4 | Knowing how to activate the facility fire alarm | |||
5 | Trying to extinguish a fire only when obviously within the capacity of the equipment available (extinguisher or hose) | |||
6 | Activating the fire alarm when available equipment is not sufficient to suppress a minor fire. | |||
7 | Maintaining a watch for at least 1/2 hour after completion of welding, hot tap or other hot work until the area has been inspected and found to be free of leaks and ignition sources (fires, hot spots or smouldering materials) | |||
35 | Note: Facilities may choose to require subsequent follow-up observations to check for leaks. | |||
EACH OF THE FOLLOWING CONSIDERATIONS SHOULD BE SATISFIED BEFORE WELDING: | Date | Time | InitialsChecked by | |
1 | Are the welders qualified for the approved welding procedure (specification) to be used? | |||
2 | Is a preheat of the weld area required? | |||
3 | Is the fitting properly positioned to prevent misalignment of the hot tapping machine? | |||
4 | Have the pressure and temperature of the contained materials been reduced as much as the process operation will allow? | |||
5 | Have the flow, pressure, and level considerations of 6.3, 6.9 and 9.1 been considered? | |||
EACH OF THE FOLLOWING CONSIDERATIONS SHOULD BE SATISFIED BEFORE CUTTING: | ||||
1 | Has the weld been inspected and tested? | |||
2 | Has the hot tap fitting been pressure tested? | |||
3 | Have the hot tap valve, packing, gasket, and bolts been checked for leakage? | |||
4 | Have the packing or seals on the hot tapping machine been checked? | |||
5 | Has the bleed-off valve been checked to assure it will hold, is operable, and is not obstructed? | |||
6 | Are all bolts on the pilot and cutter bit tight? (e.g., torqued to specification) | |||
7 | Is the coupon catcher on the pilot bit? | |||
8 | Is the valve centred on the flange? | |||
9 | Has cutting depth been calculated to avoid cutting the opposite side of the pipe? | |||
10 | Has the boring bar been run through the valve to assure free passage? | |||
11 | Have the hot tapping machine and valve been purged, if recommended? | |||
EACH OF THE FOLLOWING CONSIDERATIONS SHOULD BE SATISFIED BEFORE REMOVING THE HOT TAP MACHINE: | ||||
1 | Have the manufacturer\’s instructions been followed to be sure that the boring bar is fully retracted before closing the hot tap valve? | |||
2 | Has the hot tap valve been closed? | |||
3 | Has the bleeder valve been opened? | |||
4 | Has all of the pressure been bled from the hot tapping machine before removing the bolts from the flange? | |||
5 | Have provisions been made to contain or control any liquid or gas in the hot tapping machine? | |||
AFTER REMOVING THE HOT TAPPING MACHINE | ||||
1 | The hot tap machine should be cleaned, removing the hydrocarbons/chemicals from the line or equipment. | |||
2 | All rags, absorbent pads, and other cleaning materials must be disposed of properly. | |||
3 | When the work is completed, a follow-up job site visit may be done by operations and craft personnel to see that: | |||
3a | The work is complete, | |||
3b | No safety hazards have been introduced during the work activity. |
7. References
- API RP 2201: Safe Hot Tapping Practices in the Petroleum & Petrochemical Industries
- ASME B31.4: Pipeline Transportation Systems for Liquids and Slurries
- ASME B31.8: Gas Transmission and Distribution Piping Systems
- ExxonMobil GP 03-01-04: Hot Tapping
- SHEL DEP 31.38.60.10-Gen: HOT-TAPPING ON PIPELINES, PIPING AND EQUIPMENT