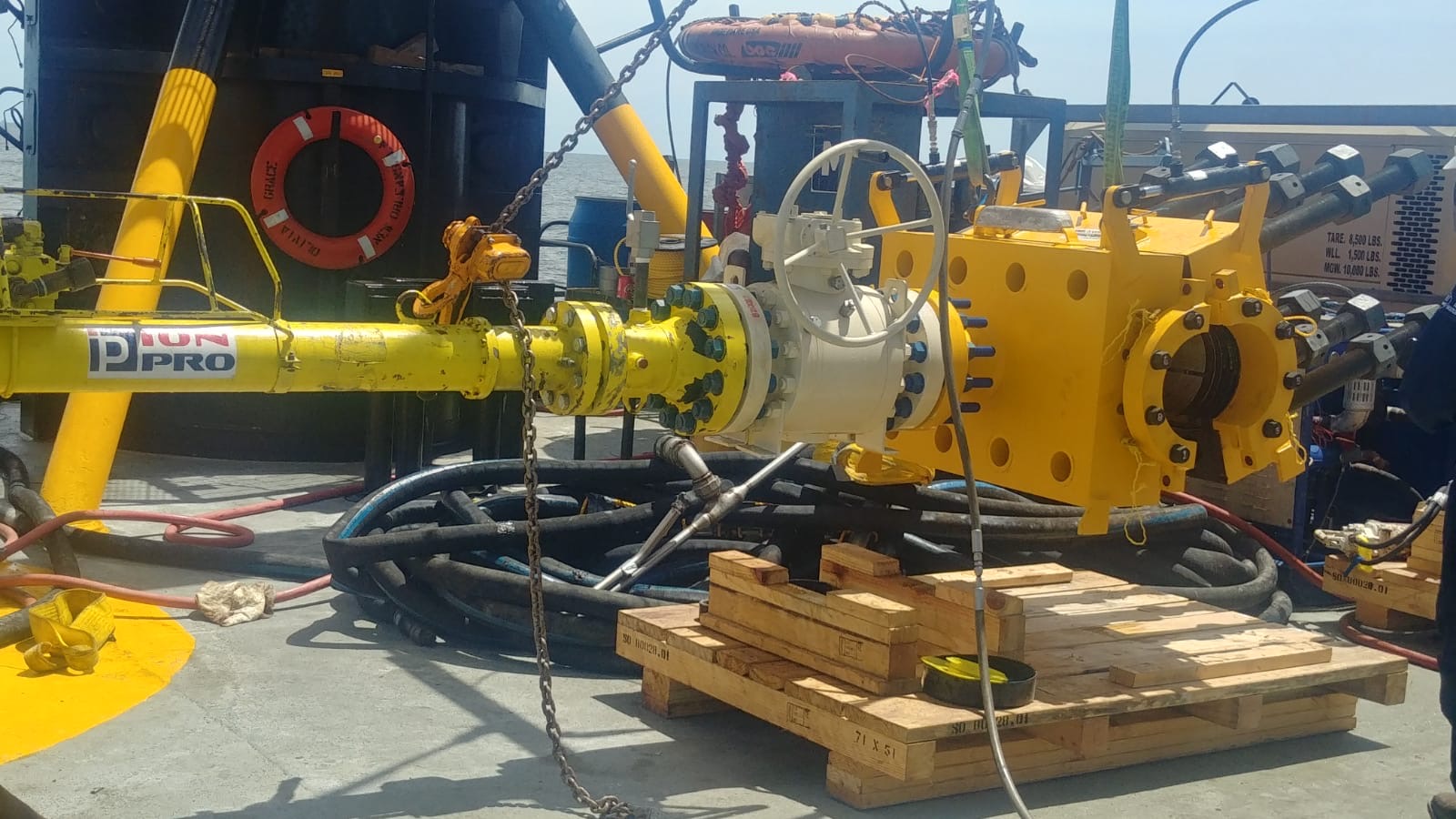
In-Service Welding
for Oil & Gas Pipelines, and Plants.
ION PRO Services provides a wide range of qualified in-service welding procedures based on API 1104 Appendix B or ASME IX acceptance criteria.
Hot Tap and Line Stop In-Service Welding Services
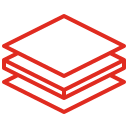
Materials
Stainless Steel and Carbon Steel
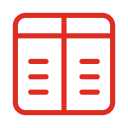
Grades
B, X42, X52, X60, X65 and X70
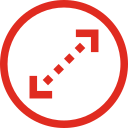
Pipeline Size
Up to 48” in diameter
Our Recent In-Service Welding Projects
What to expect during every project?
- Perfect safety record
- Zero pipeline interruption even in extreme environments
- Simplified data sheets
- Easy scheduling
- Fast quoting process
We’re ready to work.
Choose ION PRO Services for Your Next Pipeline In-Service Welding Project
At ION PRO Services, our welders have extensive experience across the globe to safely perform in-service welds in the most demanding conditions.
Our highly trained team is ready to provide:
- Pipeline material up to and including X70
- In-service welding of welded repair sleeves (Type A or B)
- In-service welding of hot tap and line stop fittings
- On-site safety analysis
Additionally, we provide PRCI Thermal Analysis Modelling on request.
Our focus is to execute the right plan to produce desired results our clients are looking for. Rest assured; you are in safe hands with ION PRO.
F.A.Q.
We are responsive to your requests and value your questions. ION PRO Services has proudly served clients seeking turnkey hot tap and line stop services as qualified experts with precision and excellence, with extensive experience in the industry.

Contact Us
Address
21233 FM 529,
Cypress, Texas, USA, 77433-5139
Phone number
Email Address